API Pipe
Product
API Pipe
Apart from BIS licenses, SWASTIK PIPE LIMITED also enjoys the confidence of API Authorities and has been possession API-5L license to mark API Monogram on its products.
At our Kosi Kalan Factory, we are manufacturing and supplying ERW Pipes in the size range of 3” dia to 10” dia in strict conformity with API-5L, PSL-1 & PSL-2 Specifications and Grade A, B, X-42, X-46 and X-52.
Our products are put to a series of stringent quality control tests before being considered fit for supply. Our products are automatically non-destructively tested with latest electronic equipment like Eddy Current Tester and Ultrasonic Testing Machine.
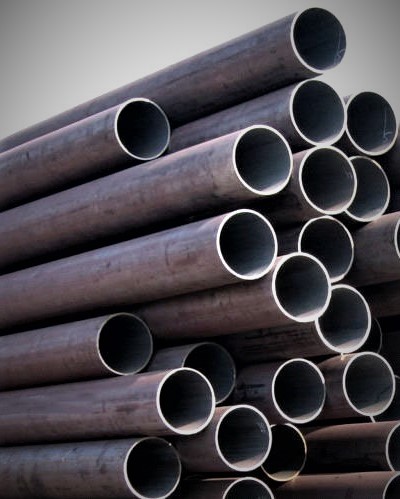
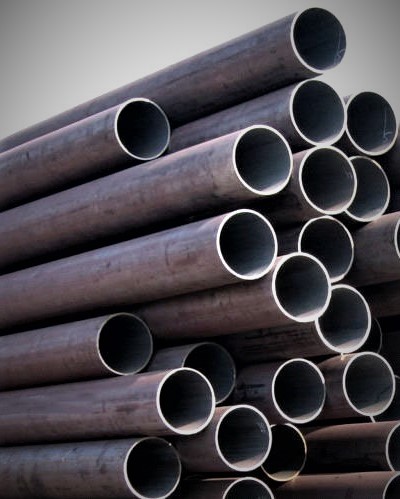
Manufacturing Process
STEP – 1
Material
Material received from SAIL / ESSAR Steel Ltd. / Lloyds / ISPAT or other any approved vendor. The steel shall be fully conformed to the API 5L / IS Standard Specification or as per Customer’s Specification. Testing/ Checking and Identification of Raw material shall be done as per API 5L / IS Standard Specification
STEP – 2
Edge Preparation & Milling
Edges of Coil / Skelp are form in edge breaking unit at initial stage so that perfect forming is achieved at welding area. Strip edges are given mill cut on both sides with edge milling machine to make the edges clean and square for perfect butt welding with high frequency. It shall be done before passing the strip to forming process.
STEP – 3
Forming of Pipe
Strip is passed in number of horizontal rolls after edge breaking and form cages supported by vertical rolls to receive an open edge round tube before welding. At the final stage of forming, rolls are provided with guide fins to have a proper proportionate gap and correct entry in welding roll
STEP – 4
High Frequency Welding
Finally the pipe shape performed after forming process, it passed through welding heads followed by the seam guide. The process of welding is based on ERW process. Electric welding shall be performed with a minimum welder frequency of 200 KHz. The fusion takes place through a roll assembly set for proper welding. Bead trimming shall be done as per API 5L / IS Standard or as per Customer Specification.
STEP – 5
Seam Normalizing
Normalizing is carried out on weld and HAZ after welding at the temperature of 8500 C to 9000 C. The temperature of seam normalizing is monitored by a non contact indicator having the digital display along with recorder. Equipment: Seam Normalizer Capacity : 500 KW
STEP – 6
Sizing
A set of sizing roll is ahead of cooling zone, water cooled pipe is passed through sizing rolls which control the Ovality and required dimensions, which is finally verified with measuring instruments as specified in relevant Specification.
STEP – 7
NDT Testing (Eddy Current)
Eddy current testing is the process of inducing small electrical currents in an electrically conductive article and observing the resultant reaction between the magnetic fields involved. Equipment: Eddy Current Flaw Detector (PC based)
STEP – 8
Finishing of the Pipes
Finished pipe are cut to required length by cut of carriage. Thereafter both ends of pipes are beveled by the end facer. Finally each pipe are checked for its Outer diameter, Inner Diameter, Thickness, Straightness, and length.
STEP – 9
Hydro Testing
After completing all the above process, all pipes transferred to the hydro testing bench. The test pressure shall be given to the pipes as per relevant specification or as per Customer Requirement.
STEP – 10
Galvanizing Process
Hydro Test passed pipes are send for Hot Dip Galvanizing confirming to various Indian Standard / International Standard.
STEP – 11
Marking
Marking on the pipes shall be paint stenciled as stipulated in API 5L/ IS Standard or as per the customer’s requirement, on each length of the pipe
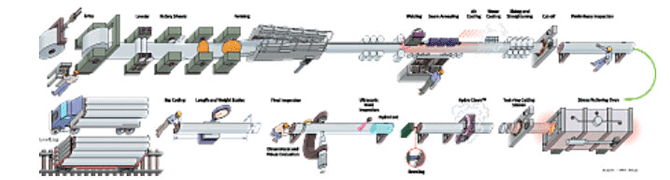
APPLICATIONS & SPECIFICATION
Water, Gas & Sewage pipes
Structural Purposes
Idlers / Conveyors
Water wells (casing pipes)
Electric Poles
Automotive Purposes
Air, Steam, Oil & Gas transmission
Scaffolds
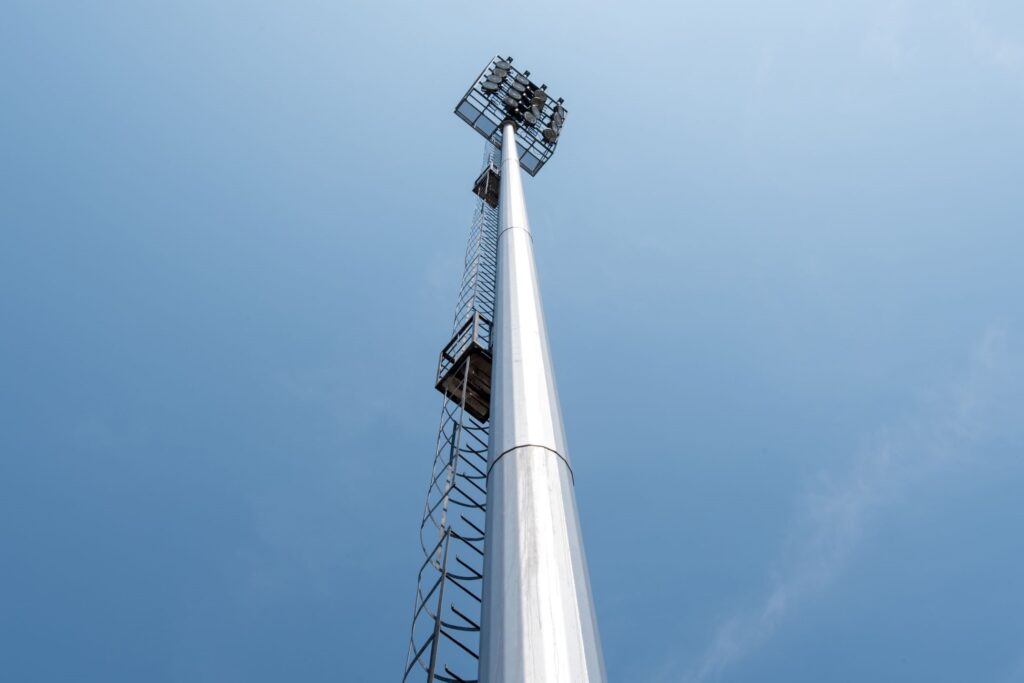